Home>Bearing knowledge>Single-stage single-suction centrifugal pump bearing smoothing method transformation |
/*728*90 created on 2018/5/16*/ var cpro_id = "u3440131";
Modification of single-stage single-suction centrifugal pump bearing smoothing method
Source: China Bearing Network Time: 2014-02-22
/*250*250 was created on 2017/12/25*/ var cpro_id = 'u3171089'; |
IS series single-stage single-suction centrifugal pump; due to the description of the reason; the rolling bearing used in the centrifugal pump is smooth with oil; the dynamic seal is very serious; the safety and stability of the equipment must be kept; the author has worked in several years; The small reform of the small leather has achieved a certain role. However, the problem of leakage has not been completely solved; after the theory, the oil is smooth and smooth and smooth; the effect is outstanding.
The smoothness of the centrifugal pump rolling bearing is mainly to reduce the friction power consumption; reduce the wear rate; together, it also plays the role of cooling, dustproof, rust prevention and vibration absorption. To make the equipment smooth is to ensure the normal operation of the equipment. Reduce equipment wear; avoid equipment problems Reduce power consumption; extend the repair cycle and use useful methods of life.
1. The process of smoothing the transformation
1.1 The felt seal is changed to a single-layer skeleton oil seal. The original bearing housing seal is sealed with felt. The leakage is very serious; the fuel consumption of each pump is about 300kg/a; a lot of oil is formed; the oil on the ground is thick.
In order to modify this oil leakage condition; change the felt seal to the skeleton seal; the method is as follows:
1 The inner and outer end caps of the bearing box are processed; the car has a round hole of Φ65mm and a depth of 12mm; a frame oil seal with a standard of 45mm×60mm×12mm is suitable.
2 Remove the felt; sneak in the skeleton oil seal with a hammer; and correct equipment.
After the transformation; the equipment works normally; the oscillation displacement is about 0. 04mm; the external temperature of the bearing is about 50 °C; the annual consumption of oil for each pump is only about 50kg. The pump room is clean and hygienic; the bearing is formed due to lack of oil. The shaft damages the attack; the equipment is working without defects.
1.2 The single-layer skeleton oil seal is changed to the double-layer skeleton oil seal in order to make the leakage amount more and more reduced; according to the layout condition of the bearing box end cover; the transformation plan is also proposed; the inner hole of the bearing box end cover is processed into the Φ65mm through hole. The layer skeleton oil seal is changed to a double layer skeleton oil seal.
The test work indicates that this method is very useful in the short-term to avoid oil leakage. However, it will work for 6 months in the future; the leakage of the skeleton oil seal will increase the leakage.
2, the shortcomings of the skeleton oil seal to change the felt oil seal to the skeleton oil seal; the use of 4a; although the effect is better; but there are also significant shortcomings.
In practice; because the life of the skeleton oil seal is short; the demand is often replaced; when replacing the skeleton oil seal; the demand will completely collapse the equipment; on the one hand, the labor intensity of the workers; on the other hand, during the equipment repair and repair; sometimes the impeller is formed Damage to parts such as bearings; does not meet the economic management requirements of the equipment; but if it does not change the oil seal; forms a leak; is not conducive to sealing; also directly affects the bearing life. Totally; theoretically proved: the skeleton oil seal does not completely solve the bearing housing of this layout Oil spill problem.
3, smooth grease instead of smooth oil; cheap and no leakage of sealing equipment has not yet; some sealing effect is good; but expensive; economically not feasible. Through investigation and research; resolution of the bladder test with smooth grease instead of smooth oil to smooth .
3.1 The transformation method takes into account that the pump shaft power is only 18.5kw; the flow rate is only 200m3/h, the pump speed is 1450r/min; the line speed is 3.4m/s. From the above two points; smoothing with smooth grease is feasible. .
3. 2 The specific method is as follows: 1. Discharge the oil in the fuel tank; remove the bearing housing.
2 Turn the end caps and oil drain holes on both ends of the bearing box to open; to remove the air inside the box.
3 Use a grease gun to fill the lithium grease from the oil filler hole into the bearing housing; add the smooth grease from the two caps and the oil drain hole; consider filling; and tighten the bearing end cap and the oil drain plug. 2. Use the hand to drive the car; make the smooth grease evenly spread in the box.
After starting the pump; open the outlet valve; make the pump work under normal conditions; supervise the temperature and oil quality of the two bearings of the pump. Monitor the temperature with an infrared thermometer. After the transformation, the oscillation displacement is about 0. 04mm.
The smooth grease oil is outstanding and unchanged; the pump works normally; it can be seen from the temperature monitoring data and the oscillation monitoring data; it is feasible to replace the smooth oil with smooth grease; it can be applied on the same type of pump.
3. 3 smooth grease smoothing smooth grease is not easy to leak; it is conducive to the smoothness of the water pump bearing; ensure the safe and stable operation of the pump; greatly reduce the amount of fueling and refueling. Not only save fuel; but also reduce the labor intensity of workers. Specifically:
1Save oil cost. Applying smooth grease, each pump costs 9kg/a; the cost is 63 yuan/a. The oil consumption is 4kg/month under the skeleton oil seal; the cost is 200 yuan/a. Each pump can save 137 yuan / a; greatly reduced the smooth cost.
2 reduce maintenance costs. The average life of the skeleton oil seal is 4 months; to replace the skeleton oil seal; to repair and repair 3 times a year; to change the lithium base grease; reduce labor costs, material costs, machinery costs; and avoid overhaul Damage to equipment parts formed during the process.
3 extends the equipment working cycle. It is monitored from the aspects of oscillation and temperature; it has good sealing performance with smooth grease; the bearing works well; the service life of the bearing is extended.
4 improved the post environment.
Totally; replace the mechanical smooth oil with smooth grease; it is practical for this kind of water pump with low speed and low flow rate; and it has significant economic and environmental benefits; it is a useful method to make the equipment economically and reasonably work.
Recommend to friends comments close window
Bearing related knowledge |
The influence of TIMKEN bearing material on its lifespan. How to improve the service life of the bearing roller of the shaft, housing and bearing? Conditions to ensure "IKO bearing stability work"
|
This article links to http://
Please indicate the bearing network http://
Previous:The basic layout and effect of rolling bearings Next: Analysis and diagnosis of locomotive rolling bearings
Aluminum Oxide Abrasive Paper is generally used for wood grinding and metal grinding. It can be divided into two parts: Hand Use Abrasive Paper and machine use Abrasive Paper. Some abrasive paper are the Waterproof Abrasive Paper.
If you have any questions, please contact with us directly. The Abrasive Cloth are produced with high quality and good appearance. Welcome you can visit our factory for inquiry. Please send mail directly to us.
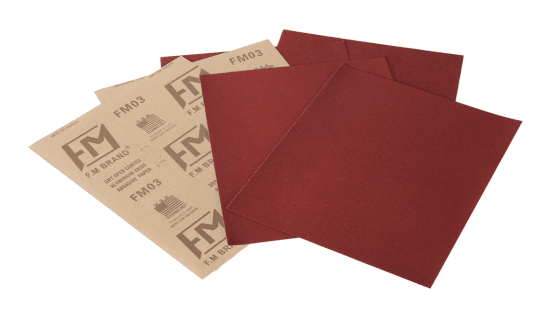
Aluminum Oxide Abrasive Paper
Aluminum Oxide Abrasive Paper,Hand Use Abrasive Paper,Soft Abrasive Paper,Anticlog Abrasive Paper
Jiangsu Fengmang Compound Material Science & Tech Group CO.,LTD , http://www.fmabrasive.com