The one-million-kilowatt nuclear island steam generator is a critical pressure vessel, designed to withstand high-pressure water at 15.4MPa during operation. As a first-grade safety component, uneven wall thickness can lead to stress concentration and potentially serious hidden accidents. This paper focuses on the challenges of achieving consistent wall thickness across both the inner and outer surfaces of the elliptical upper section.
**First, Analysis of Part Geometry and Accuracy Requirements**
The part has a top-and-bottom structure, with the upper section combining a cylinder and a conical surface, while the lower part features a spherical-like shape. The internal surface exhibits an elliptical pattern, and the external surface connects to an R125mm arc. The minimum required wall thickness is 98 mm (see Figure 1).
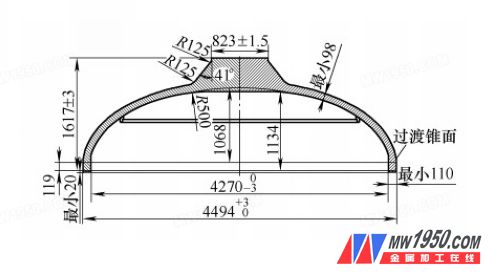
Figure 1: Upper head
The overall size tolerance is 3mm, and the surface roughness should be within Ra=3.2 μm, which aligns with the economic accuracy of CNC machine tools. However, maintaining equal wall thickness on the spherical surface presents a unique challenge. According to GB/T1804-2000, the linear dimension limit deviation is ±0.3mm. Therefore, the wall thickness tolerance must remain within 0.6mm, with deviations not exceeding ±0.3mm. The primary difficulty lies in controlling the tolerance and accuracy of the spherical wall thickness, especially in terms of how the machining system distributes these tolerances.
**Second, Main Error Items and Control Measures in the Process System**
Achieving the required geometric accuracy for large spherical parts composed of multiple shapes is a complex process. Several factors influence the wall thickness tolerance, including tool system errors, machining method errors, and numerical control mathematical model inaccuracies.
**1. Influence of Tool System Errors on Surface Thickness Accuracy**
As a rotary part, this component is best machined using a vertical double-column or single-column CNC lathe with a rotary table. Key factors affecting accuracy include the precision of the rotary table, the vertical motion trajectory of the tool holder, the geometric position accuracy of the table, positioning and repeatability accuracy, tool rigidity, and thermal deformation caused by cutting heat. These elements collectively impact the accuracy of inner and outer curved surfaces, reducing the available tolerance range. The target is to reduce the integrated error to T/5 (see Figure 2).
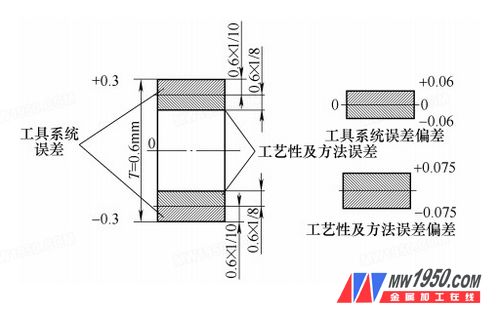
Figure 2: Schematic diagram of machining system tolerance distribution
To achieve this, equipment accuracy adjustments are made, such as ensuring the worktable rotation accuracy is 0.05mm/360°, tool holder perpendicularity is 0.03mm/1000mm, and positioning accuracy is 0.015mm/1000mm. Thermal effects from cutting are minimized, and the clamping force is adjusted before final finishing to enhance system stiffness. The integrated error is controlled to 0.12mm with a deviation of ±0.06mm.
**2. Influence of Machining Technology and Method on Surface Thickness Accuracy**
The CNC machining process requires precise alignment of the positioning reference between different stations. For large parts, the finishing stage often reveals issues with positioning stability and reference coincidence. Two working stations are typically used to machine the inner and outer contours (see Figure 3). While station 1 offers good positioning stability, station 2 faces challenges due to a high center of gravity and poor positioning surface contact. This leads to misalignment and uneven wall thickness, further narrowing the tolerance range.
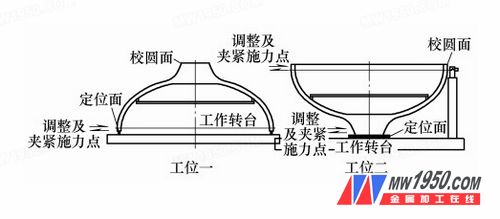
Figure 3: Two station positioning instructions
To address this, the process sequence is optimized, with the inner surface machined first to establish a stable reference for the outer surface. This approach ensures that the design and process references coincide, improving overall accuracy.
**3. Definition of the Numerical Control Machining Mathematical Model and Its Impact on Wall Thickness Accuracy**
The mathematical model for NC machining is crucial. If the inner surface follows an elliptical equation y = (b/a)√(a² - x²), the outer surface would need to follow a concentric ellipse Y = (B/A)√(A² - X²), where A = a + c and B = b + c. However, this results in inconsistent wall thickness due to differing ellipticities. To maintain equal thickness, the outer surface must follow a spline curve instead of an ellipse. By increasing the order of the spline curve and inserting more points, the contour accuracy is significantly improved, leading to more uniform wall thickness (see Figures 8 and 9).
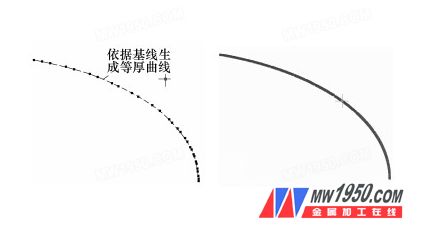
Figure 8: Third-order spline curve
Figure 9: High-order sub-interpolation spline curve
**Third, Conclusion**
(1) Controlling tool system errors, machining method errors, and NC mathematical model inaccuracies is essential for ensuring the quality and stability of the elliptical head. These factors directly affect the final part accuracy, and proper control is achievable through careful planning and execution.
(2) By refining the mathematical model and using dense point insertion in the spline curve, the influence of precision errors can be minimized, resulting in a more accurate and uniform wall thickness.
(3) This process has been successfully applied in the manufacturing of the first domestic CPR1000 evaporator, with six steam generators produced locally. The parts meet all technical specifications, and the wall thickness control is within 0.15mm, proving the effectiveness of the proposed method.
PTO Track Oil Gear Pump
We have two types PTO pumps, PTO gear pump and PTO vane pump. this kind of pump can driven by truck engine and electric motor. Our PTO pump been used to transfer diesel fuel oil. engine oil, lube oil, lubricating oil , gasoline etc oil. pump small size, great strength, easy operation, low price.
Pto Track Oil Gear Pump,Pto Gear Oil,Gear Oil Pump Tool,Pto Track Oil Gear Pump Engine
Hengshui Yuanhan Trading Co.,Ltd , https://www.yuanhanpump.com