Abstract "Nanotechnology Concept" At the 9th China International Machine Tool Show [1], NantWin Abrasives with the "Nanotechnology Concept" introduced by Wintersell are thought-provoking, and the bonding agent is nano-coated. Recrystallized glass bond 602W, in...
"Nanotechnology concept"
At the 9th China International Machine Tool Show [1], NantWin abrasives with the concept of "nanotechnology" introduced by Wintersell are thought-provoking. The binder is a recrystallized glass bond with nano-coating. 602W, in the manufacturing process of ceramic bond abrasives, the formation of similar glass crystal chains in the binder can not only improve the strength of the abrasive tools, but also adapt to high-speed grinding, and more importantly, reduce the bonding agent in the abrasive tools. Improve the porosity of the abrasives, while avoiding the adhesion of the abrasives, so that the performance of the abrasives is greatly improved.
I. Experimental study on nano-colloidal dynamic pressure cavitation jet polishing
Jet polishing is a new technology developed in the 1990s. It uses fluid as a polishing tool and is considered to be one of the most promising methods for processing complex hard and brittle material products [2]. The initial jet polishing technique utilizes abrasive jets. In 1998, Dutch Fahnle OW et al. applied abrasive jet polishing to optical surface processing, to obtain a working surface with a roughness value of Ra5nm [3]. Later, Messelink Wilhelnms ACM and other liquid-jet polishing spherical experiments, the new material in the polishing process depends on the sharpness of the abrasive and its kinetic energy conclusion [4].
Domestic Wang Jiansheng believes that the abrasive jet processing abrasive particle size is 1/3-1/4 of the nozzle diameter. Fang Hui of Suzhou University studied the main process factors and processing mechanism affecting the polishing effect of abrasive jet [5]. Zhu Hongtao studied the polishing mechanism of abrasive jets. It is believed that the removal of materials mainly relies on the erosion of abrasive particles, and the water jet only plays a supporting role [6].
Recently, Harbin Institute of Technology Song Xiaozong et al. proposed nano-gel colloidal jet polishing and nano-particle colloidal solution instead of ordinary abrasives to obtain an ultra-smooth surface with roughness less than Ra0.6nm [7,8].
Nanoparticle colloidal jet polishing is the use of the interface chemical reaction between the nanoparticles and the surface of the workpiece to achieve the removal of the workpiece material. The material removal is in the atomic scale, so the disadvantages that the mechanical action material removal method cannot avoid, such as the subsurface, are avoided. Damage, surface atomic lattice damage, etc. [9].
However, the processing effect of nano-particle colloidal jet polishing is too low. In order to improve the processing effect of nano-particle colloidal jet polishing, Wang Xing et al. consider introducing cavitation into nano-particle colloidal jet polishing to achieve efficient processing of workpieces and high quality. The ultra-smooth surface is therefore proposed for nano-colloidal dynamic pressure cavitation jet polishing.
Figure 5.1 is a schematic diagram of the processing system used in the experiment.
The entire system is divided into two parts: the hydraulic system provides the required pressure for processing, and the nano-colloid system relies on the pressure provided by the hydraulic system to process the workpiece.
Figure 5.1 Schematic diagram of the experimental system
Figure 5.2 shows the simulation results of the cavitation of the normal jet and cavitation jet field. The results show that the rotary jet nozzle produces a wide range of cavitation zones, and the volume fraction of the second phase (cavitation) is as high as 86.9%, and the volume fraction of the second phase in each cavitation zone is above 20%; The edge of the part forms a certain amount of vacuoles, and the flow field cavitation phenomenon is not obvious.
Figure 5.2 nozzle flow field simulation diagram
Observing the contours of the two polishing methods, no matter whether it is ordinary conical nozzle polishing or rotary nozzle polishing, the material removal at the center of the polishing pressing region is less, and the deepest portion is located at the same distance from the polishing center.
The vertical distance between the lowest point of the cross-sectional profile of the processing zone and the unmachined surface was measured to obtain the depth of removal of the processed material within 2 hours. The result is shown in Figure 5.3. The removal depth achieved by cavitation jet polishing for 2 h is 0.26 μm; the removal depth of ordinary jet polishing is slightly smaller, 0.23 μm.
Figure 5.3 Depth of removal of cavitation jet polishing and normal jet polishing for 2h
The surface of the machined surface was examined by atomic force microscopy. It was found that in the same processing area, the position with higher roughness was in the central area where the workpiece material was removed less, and the surface roughness value at the most removed ring was the lowest. The analysis suggests that the cause of this result may be due to the influence of the flow state of the polishing fluid [10].
Second, low-melting high-strength nano-ceramic binder coarse-grained superhard tool
During the cooling of the sintered superhard tool, the shrinkage of the superhard particles is less than the shrinkage of the bond, so tensile stress is generated in the bond, as shown in Figure 5.4.
Figure 5.4 Schematic diagram of interface stress distribution of superhard tool particles-bonding agent
The traditional super-hard material tools are mainly composed of metal and resin binders. Due to the good plasticity and toughness of metals and resins, the tensile stress generated is much smaller than the tensile strength limit, and the stress can be relieved and relaxed by a certain plastic deformation; However, for the brittle traditional ceramic bond, because the tensile strength is relatively small and there is no plasticity, the internal tensile stress will cause serious damage to the strength of the ceramic bond, making the interface between the bond and the super-hard abrasive particles easy to produce. Microcracks and even scraping of the agglomerates cause tool waste. Therefore, studying the distribution law of bond-abrasive interface stress, alleviating or eliminating the interface stress, has a significant significance for the wide range of applications of ceramic bond superhard abrasives.
In order to improve the tensile properties of traditional ceramic binders, the interfacial stress of the particle-bonding agent is alleviated and the damage of the superhard abrasive by high temperature is avoided. Zhang Xianghong, Wang Yanhui et al. [11] introduced nanotechnology into ceramic binders, introduced nanoscale particles, platelets, whiskers and fibers into the ceramic binder matrix, and developed a new nanoceramic. The binder reduces the sintering temperature of the superhard abrasive and relieves the interfacial stress problem of the abrasive-conventional ceramic bond.
There are two types of ceramic binders used in the test: traditional binders and nano-bonders for comparative study of binder-superabrasive properties. The chemical composition is shown in Table 5.1.

Figure 5.5 shows the flexural strength of a sintered specimen of diamond/ceramic bond. It can be seen from Fig. 3 that due to the difference in thermal expansion coefficient between the diamond and the ceramic bond, the tensile stress is generated during the cooling process of the bonding agent, and as the diamond particle size increases, the tensile stress increases, and the sample is folded. In addition, due to the size effect, the nano-ceramic binder has lower softening temperature and better toughness than the ordinary binder, and the low softening temperature makes the sintering of the nano-ceramic more dense than the sintering of the ordinary binder, and is good. The toughness increases the tensile stress tolerance of the nanobinder, so the strength of the diamond/conventional bond sample is much lower than the strength of the diamond/nano bond sample under the same preparation conditions.
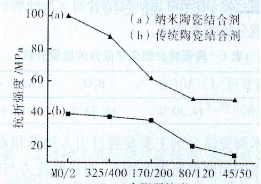
Figure 5.5 Effect of diamond particle size on the strength of ceramic bond diamond composites
in conclusion:
(1) As the superabrasive grain becomes coarser, the tensile stress accumulated at the interface of the bond diamond increases, and the flexural strength of the sample decreases.
(2) Compared with the traditional ceramic binder, the nano-ceramic binder has a small interfacial bonding stress under the same experimental conditions, thereby improving the flexural strength of the specimen.
(3) The practice of industrial application proves that the use of nano-ceramic binder can greatly improve the strength, toughness and wear resistance of the product, and the stability and reproducibility of the experimental results are good, and the industrial application has been successfully obtained.
Third, the grinding performance of nano-SiO2 modified diamond flexible grinding wheel
The tensile strength refers to GB/T2568-1995, and the shape and size of the sample are shown in Figure 5.6.
Figure 5.6 Tensile strength sample shape size chart
   The tensile shear strength refers to GB7124-86, and the sample shape size is shown in Figure 5.7.
Figure 5.7 tensile shear strength sample shape size chart
1 Influence of ultrasonic dispersion time on mechanical properties of resin adhesive
The uniformity of dispersion of nanoparticles in the resin matrix is ​​the determining factor of the effect, and the dispersion uniformity is mainly determined by the superdispersion time.
Figure 5.8 Relationship between ultrasonic dispersion time and mechanical properties of resin adhesive
It can be seen from the graph that when the amount of n-SiO2 added is 3% of the total amount of the resin, the tensile strength of the resin adhesive increases first and then decreases with the ultrasonic dispersion time. When the ultrasonic dispersion time is 5 min, the tensile strength and the tensile strength are not The tensile strength of the ultrasonic dispersion sample is not much different. This is because the ultrasonic dispersion time is too short to improve the dispersion uniformity. When the ultrasonic dispersion time is 15 min, the tensile strength reaches the maximum value of 40.3 MPa. Increase by 21%. This is due to the cavitation in the ultrasonic vibration, the formation of microbubbles in the liquid medium and the strong vibration waves in the instant accompanying the release of energy. The rapid formation and sudden collapse of the liquid hollow bubbles creates a short-lived high-energy microenvironment. The resulting local high temperature, high pressure or strong shock wave and micro jet, etc., can greatly weaken the nano-action energy between the nanoparticles, effectively prevent the nanoparticles from agglomerating and fully disperse, so that n-SiO2 is in the resin The size and surface effect of the matrix are fully utilized to greatly increase the tensile strength; however, the longer the ultrasonic dispersion time, the better the effect.
The experimental results show that when the ultrasonic dispersion time is 20min, the tensile strength is lower than that at 15min. This is because the continuous ultrasonic time is too long, and ultrasonic supersonic stirring occurs during ultrasonic cavitation, so that the temperature of the system rises. As the thermal energy and mechanical energy increase, the collision probability of the particles also increases, which in turn leads to further agglomeration and lower tensile strength.
For the tensile shear strength, as the ultrasonic dispersion time increases, the strength also increases first and then decreases. When the dispersion time is 15 min, the maximum value is 14.1 MPa, and the maximum tensile shear load is 4580N, which is nearly 75% higher than that without ultrasonic dispersion, which is also because the small particles of n-SiO2 enhance the tensile strength, while the polymerization shrinkage force decreases, and the bond strength between the resin and the steel sheet increases, but with the ultrasonic dispersion time The elongation of the nanoparticles increases the agglomeration of the nanoparticles, and the effect of the nanoparticles on the resin is weakened, so that the tensile shear strength is rather reduced.
2 The effect of nanomaterial addition on mechanical properties
Figure 5.9 Line diagram of the relationship between the amount of nano-added and the mechanical properties of resin adhesive
   It can be seen from Fig. 5.9 that with the increase of the addition amount of n-SiO2, the tensile strength and tensile shear strength of the nano-SiO2 are basically increased first and then decreased. When the amount of n-SiO2 added is 3%, the tensile strength is The tensile shear strength reached the maximum, which was 40.3MP and 14.1MPa, respectively, which increased by 4% and 7% respectively compared with the addition of n-SiO2. This is also because the surface of n-SiO2 particles has many active groups. Chemical bonding with unsaturated bonds in the polymer enhances the interfacial bonding between the two. At low levels, n-SiO2 acts as a physical crosslinking point in the system, increasing the crosslink density of the composite system, thereby The shear strength of the system increases.
At the same time, it was found that when the amount of n-SiO2 added was 3%, if the ultrasonic dispersion was not performed or the dispersion time was too short, the tensile strength and tensile shear strength were lower than those without n-SiO2, indicating that Adding n-SO2 particles, if not uniformly dispersed, not only fails to achieve the desired effect, but also degrades the performance of the resin adhesive itself.
Effect of 3 nanometer modification on mechanical properties of diamond-containing samples 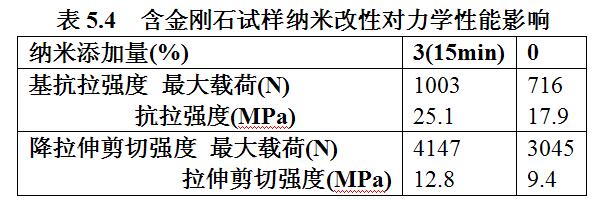
It can be seen from Table 5.4 that the tensile strength of the acrylic resin modified by 3% n-SiO2 after adding w40 diamond to the compound ratio of 2:1 is increased by 40%, and the tensile shear strength is increased by 36%. The increase is much greater than when no diamond is added. This is because the addition of w40 diamond to the resin is equivalent to the addition of micron-sized fillers, which only fills the resin matrix without chemical bonding with the resin matrix, and the surface of the diamond is highly polar, and the surface of the resin is wetted. Low in nature, when the external force is applied, the actual cementation area of ​​the loaded section is small, the strength is reduced, and the surface polarity of the diamond is large. The surface wettability of the resin is low, and the resin bonding strength is weakened more. By dispersing and dispersing the nanoparticles, the strength of the resin matrix itself is improved, and the gap between the micron-sized diamond and the resin matrix can be filled. In addition, the nanoparticles surface-treated by the coupling agent can effectively weaken the surface polarity of the diamond, so that the strength of the resin matrix is ​​not much reduced by the addition of micron-sized diamond.
Comparison of grinding performance of diamond flexible grinding wheel before and after modification 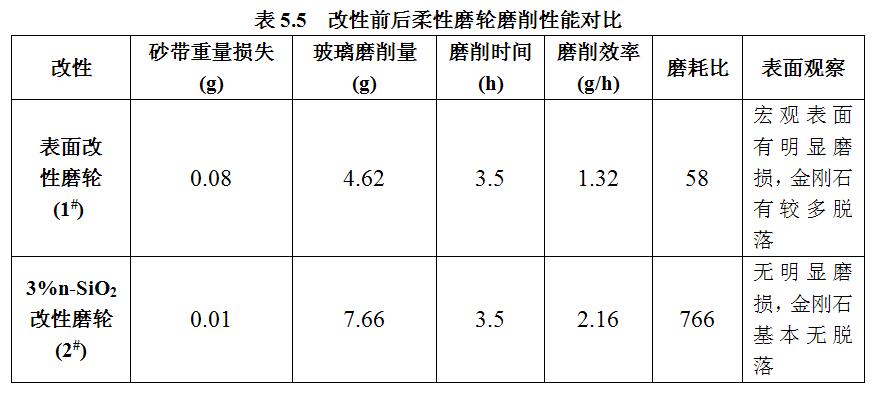
It can be seen from the results of the grinding test that the diamond flexible grinding wheel modified by n-SiO2 has no wear after grinding for 3.5h, and the grinding efficiency and wear are improved compared with the diamond flexible grinding wheel which has not been modified by the adhesive. This is because the wear resistance of the diamond flexible grinding wheel is determined by the combination of diamond and adhesive. The diamond-coated resin adhesive itself is not wear-resistant. The diamond grinding edge can not fully exert its grinding ability and reduce the life of the grinding wheel. The greater the tensile strength of the resin material, the stronger the internal cross-linking effect, the stronger the anti-stripping and friction-wearing ability, and the stronger the wear resistance, the higher the utilization rate of the diamond and the life of the grinding wheel. At the same time, corresponding to the tensile shearing effect, due to the modification of the nanoparticles, the bonding strength of the diamond to the diamond is improved, the shedding of the diamond is reduced, and the height of the diamond blade is increased, thereby improving the grinding efficiency of the diamond.
in conclusion:
1 Nano-SiO2 was modified by TL-2 aluminum-zirconium coupling agent. When the content of nano-SiO2 was 3%, the resin adhesive had the best tensile strength and tensile shear when the ultrasonic dispersion time was 15 min after 10 min mechanical stirring. The intensity was increased by nearly 21% and 75%, respectively, compared to the absence of ultrasonic dispersion.
2 When the dispersion process is mechanical stirring for 10 min, ultrasonic dispersion for 15 min, and nano-SiO2 addition amount of 3%, it has the best tensile strength and tensile shear strength, which are 4% and 7% higher than those without addition.
3 After adding w40 diamond with a rubber compound ratio of 2:1, the tensile strength of the 3% nano-SiO2 modified adhesive is increased by 40%, and the tensile shear strength is increased by 36%, so the mechanical properties of the diamond-containing sample are obvious. Modification effect.
4 The diamond flexible grinding wheel prepared by using 3% nano-SiO2 modified acrylic resin adhesive has greatly improved the grinding performance before 3.5h before the unmodified diamond flexible grinding wheel, and proved the mechanical properties of the adhesive and the grinding performance of the diamond flexible grinding wheel. Correspondence [12].
(This article is taken from Professor Wang Guangzu's "Preparation and Application of Superhard Abrasives" Chapter 5) Incense Cones
Natural Incense Cones,Backflow Incense Cones ,Incense Cones,Different Color Incense Cones
Xinhui Gangzhou Flavors&Fragrance Co.,Ltd , https://www.xhgzff.com