ã€
Abstract】 Explain the origin and characteristics of nano-diamond and the main application fields of this product at home and abroad. It focuses on the dispersion research of nano-diamond and its application in special functional coatings, and on the current domestic nano-diamond in the field of coatings. The content and direction of research and application have been prospected.
[Keywords] nanodiamond; dispersion; special coatings
1. Introduction Nanodiamond (nanodiamond) refers to diamond particles with a grain size below 100nm. In the foreign literature before 2000 or earlier, this diamond is also called ultrafinediamond (UFD), translated into ultrafine (fine) diamond, and another type is ultradiseddiamond (UDD), translated into super-dispersed diamond. . In other domestic academic literature, it is often called “nano-diamondâ€. After 2000, influenced by the international nanomaterials, domestic scholars basically began to use the name "nano-diamond." By this time, the name of this diamond was basically unified, and everyone called it "nano-diamond." For more than half a century, material researchers have developed several methods of artificially synthesizing diamond. In 1954, General Electric Company of the United States first used graphite as a raw material to synthesize diamonds using static high-pressure and high-temperature methods with the participation of metal catalysts. DeCarli successfully produced nanodiamonds in 1961 using a dynamic high pressure method (explosive method). In 1975, Fedoseev et al. used a low pressure chemical vapor deposition (CVD) method to produce a conventional diamond film. In the early 1980s, former Soviet scientists and technicians took the lead in synthesizing nanodiamonds using detonation of negative oxygen balance explosives. In 1983, Fedoseev and Derjaguin reported on a diamond synthesis method using a laser to irradiate a solid phase carbonaceous material. In 1992, Ogale et al. used a ruby ​​laser to irradiate a graphite target soaked in benzene to synthesize diamond, and further extended the laser-induced solid-state conversion synthesis diamond into a liquid medium environment. This paper mainly describes the research and application of nano-diamonds at home and abroad, especially in the application of dispersion technology and special coatings, and prospects for the application of nano-diamonds in China's coatings industry.
2. Synthesis and surface state analysis of nanodiamonds At present, the methods of artificially synthesizing diamond mainly include static pressure method, deposition method and dynamic pressure method. The dynamic pressure method uses the high-pressure and high-temperature conditions generated instantaneously to generate diamond. According to the raw materials of synthetic diamond, it can be divided into the following three categories: the first type is the shock wave method, and the graphite target plate is struck by the high-speed flying piece to make the graphite in the impact process. In the micro-scale diamond generation, the first research in this field in China is the Institute of Physics of the Chinese Academy of Sciences. The second type is the explosion method or the detonation method, which combines graphite with high-energy explosives to compress graphite into diamonds during the detonation of explosives. The last category is the detonation product method, which uses a negative oxygen balance explosive detonation to obtain a diamond having a grain size on the order of nanometers. Figure 1 is a partial apparatus for preparing nanodiamond by detonation of DiamondCentreLtd., Russia.
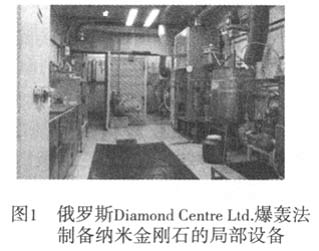
The biggest difference between the detonation method and the former two dynamic pressure methods is that the first two methods need to provide a carbon source, and the prepared diamond particle size is mostly on the order of micrometers or more. The last method, which does not require the provision of an additional carbon source, provides both high-pressure and high-temperature conditions as well as a source of carbon. The basic principle of the preparation of nanodiamond by detonation method is as follows: the negative oxygen balance explosive explodes in the protective medium environment, and the excess carbon atoms in the explosion process undergo a series of physical and chemical processes such as aggregation and crystallization to form a nanometer scale carbon particle group, wherein It includes a diamond phase, a graphite phase, and amorphous carbon. After selective oxidation chemical treatment, the non-diamond phase is removed to obtain a nano-scale diamond powder. The research on detonation and synthesis of nano-diamonds in China is relatively late. From about 2000 onwards, the research on nano-diamonds has gone from laboratory level to large-scale production. Although it started late, the growth of nanodiamond research and production is very high, and the enterprises that can produce nanodiamonds on a large scale have sprung up. China's major companies and companies producing nanodiamonds are: Gansu Jinshi Nanomaterials Co., Ltd. (formerly Gansu Lingyun Nanomaterials Co., Ltd.; Shenzhen Jingangyuan New Materials Development Co., Ltd.; Beijing Jiulong Huayuan Diamond Ultrafine Powder Research Institute; Changsha Research Institute of Mining and Metallurgy; Tianjin Ganyu Superhard Technology Co., Ltd; Shandong Jinjinchi Nano Technology Co., Ltd.; Beijing Bonas Co., Ltd.; Henan Hengxiang Diamond Abrasive Co., Ltd.; Beijing Guoruisheng Technology Co., Ltd.; Zhengzhou United New Materials Company; Shanghai Kia Grinding Technology Co., Ltd.; Guangzhou Aipu Nano Technology Co., Ltd.; Shaanxi Yilin Industrial Co., Ltd. The content of C element and diamond phase in nanodiamond powder are two different concepts that need clarification. According to the test results of the prepared nano-diamond powder, the main element in the nano-diamond is C, and the mass fraction varies depending on the preparation method, but most of them are between 85% and 90%. Other more elemental impurities such as H ≤ 1%, N ≤ 6%, O ≤ 10%, and other impurities, such as Al, Si, Ca, Fe, etc., the content of which is 10-4~10-6 From the test results in Table 1, it can be seen that in the preparation of nanodiamond, the use of explosive containers of different materials has an absolute effect on the content of metal impurities in the nanodiamond. Table 1 Contents of other impurity elements in the nanodiamond x10
-6 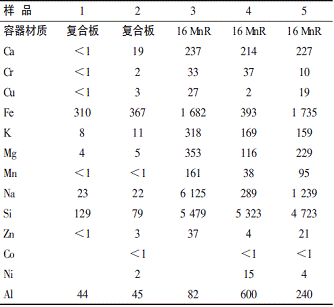
X-ray photoelectron spectroscopy (XPS) was used to analyze the elemental composition of nanodiamond materials. The main elements of nanodiamond surface were C, O and N, of which C was 90.65%, O was 8.09%, and N was 1.14%. In addition, there are S, Cl, etc. The N of the nanodiamond surface is in a variety of chemical environments, the main chemical state of which is in the form of amine groups.
3. Application fields of nano-diamonds and application status at home and abroad Compared with other materials, diamond has many excellent properties. Among all materials, diamond has the highest hardness, the highest thermal conductivity, the highest sound
Transmission speed, and high. Wear resistance and low friction coefficient are both electrical insulators and good thermal conductors. After doping, they can be excellent PN-type semiconductors with wide band gap, high hole mobility and widest permeability. The optical band (0.225μm to far infrared) is the above-mentioned characteristic which provides a solid technical foundation for its wide application in modern technology and industry, and is also an important reason why other materials are incomparable. 3.1 Lubrication Technology Field Recent studies have shown that the addition of nanodiamonds to lubricating oils exhibits the following advantages. (1) Improve the quality and competitiveness of products; improve the working life of transportation tools and installations; and save lubricant materials. (2) The friction momentum is reduced by 20% to 40%. (3) Friction surface wear is reduced by 30% to 40%. (4) Rapid running-in of the friction pair. The unit consumption of nanodiamond: 0.01 to 0.20 kg in 1000 kg of lubricating oil. The peculiar effect of nano-diamond in lubricating oil is beyond the expectations of many people. It is not only used to make engine oil, but also to make worm oil, gear oil, hydraulic oil, vacuum pump oil, high-speed mechanical oil, machine tool oil and so on. According to authoritative sources, in 2002, China consumed about 4.0×106 tons of lubricating oil, with sales of tens of billions of yuan, and increasing at a rate of 10% per year. It has been predicted that the modification of nano-diamonds will form a boom in the near future and truly industrialize nanotechnology. We look forward to the emergence of a new nano-lubricant industry with Chinese characteristics. 3.2 Grinding and polishing field Grinding and polishing is a very important application area of ​​diamond. Abrasives and abrasives made of "Carbonado" diamond micropowder for fine ceramics, integrated circuit chips, various gemstones, ferrite heads, quartz plates, hard alloys, optical lenses, hard disks Finishing and polishing of the surface of various hard materials such as magnetic heads. Compared with single crystal diamond powder, it has high processing efficiency, long service life and high surface finish, showing excellent performance. After polishing with the domestic spherical "Carbonado" polycrystalline diamond, the surface roughness of the workpiece can be reduced to below 0.6 nm, showing its unique superiority. More than a decade ago, the pass rate of US chips was often less than 50%. At present, the pass rate of chips produced in the first-class factories in the United States is over 80%, and Mypolex polycrystalline diamond plays an important role in ultra-fine polishing of chips. Therefore, the spheroidal diamond micropowder will play an important role in the chip surface processing industry in the 21st century. In 1997, the world's chip production reached 150 billion, of which 15 billion were used in microprocessors. With the improvement of chip precision and the expansion of its capacity, the demand for explosive synthetic diamond micropowder to ensure the final surface precision of the product will increase simultaneously. The development of domestic chip manufacturing industry will certainly provide a huge market for polycrystalline diamond micropowder. 3.3 Electroplating technology field It is understood that the annual metal corrosion loss in the world is about 150 billion US dollars, and China's annual loss is 150 billion yuan, and metal plating is one of the ways to solve this technical problem. In recent years, diamonds have been frequently reported for composite plating, and high hardness and corrosion resistance of composite coatings have received increasing attention. However, since the general diamond particles are micron-sized or sub-micron-sized, the particles are coarse, and the obtained coating structure is difficult to meet the requirements of precision instruments, high-gloss surfaces, fine processing, and higher wear resistance. With the rapid development of nano-diamond production technology, especially the emergence of 2-12 nm diamond, the use of nano-diamond to form a composite coating is expected to make up for this deficiency. Brush plating technology is a new type of surface modification technology developed on the basis of electroplating technology in recent years, which can solve the problem of repairing mechanical parts that are difficult to solve by other technologies. The Solid Lubrication Open Research Laboratory of the Lanzhou Institute of Chemical Physics of the Chinese Academy of Sciences collaborated with the Materials Department of Lanzhou University to study the tribological properties of composite nickel brush coatings containing nanodiamonds. The results show that the coatings have excellent antifriction and wear resistance. In the test range, its antifriction and wear resistance increases with the increase of nanodiamond black powder content. China's current annual output of more than 3 billion cylinders, mainly used in automobiles, motorcycles, home appliances, mining machinery, textile machinery, shipbuilding and precision machine tool instrumentation, military and other industries, the need for nano-composite plating process upgrade. In addition, the market for decorative plating of molds and plastics and glass in China is huge. According to rough calculation, if the plating surface reaches 3.0×108m2, the thickness of the plating layer is calculated as 5μm, and 0.2g of nano-diamond is required per square meter, then the nano-diamond-metal composite The nanodiamond required for plating the additive will reach 6.0 x 105 kg. The prospect of nano-diamond composite plating is broad. 3.4 Preparation and Application of Nanocrystalline Diamond Films Since the 1980s, CVD diamond films have made breakthroughs. The conventional CVD diamond film has a large grain size, grows in a column shape, and has a rough surface. At the same time, the high hardness surface brings great difficulty to the subsequent polishing process, directly limiting the promotion and application of the diamond film and the industrialization process. Therefore, many researchers are working to improve the surface roughness and subsequent polishing techniques of conventional diamond films. With the development and maturity of CVD deposited diamond film technology, nano-diamond film coating technology came into being. The nano-diamond film has a very fine grain size of 7-10 nm or even smaller (2-6 nm), which is more than two orders of magnitude smaller than the conventional diamond film; the surface is smooth and the film friction coefficient is very small, which can reach 0.03. Moreover, the hardness of the nano-diamond film is 10% to 20% lower than that of the conventional diamond film, which is very favorable for the subsequent polishing of the film. At the same time, due to the nano-effect, the resistivity of the nano-diamond film decreases and the infrared transmittance increases, making it in microelectronics and optics. The field has great potential for application. The nano-diamond composite coating adopts CVD technology, which has the characteristics of strong adhesion and wear resistance of conventional coatings, and has the advantages of smooth surface, low friction coefficient and easy grinding and polishing of nano-diamond coating. The ideal combination. Various coating products (drawing die, powder coating die, pressing die, sizing sleeve, bearing supporter and tensile die) developed by nano-diamond composite coating technology will not only greatly improve the service life of molds and tools. , effectively reduce costs and improve production efficiency; and can fundamentally improve processing quality and improve product quality. According to reports, the nano-diamond composite coating drawing mold developed by Shanghai Jiaotong University has been industrialized by Shanghai Dating Diamond Coating Co., Ltd. The product has been applied in more than 70 production enterprises such as Jiangsu Shangshang Cable Group Co., Ltd. and Shanghai Huapu Cable Co., Ltd., which has brought significant economic benefits to the application enterprises. The newly added output value is 1.4 billion yuan and the profit is 45.1 million yuan. 60.90 million yuan, saving 35.71 million yuan. In view of the above advantages, nano-diamond films are expected to become new mold coating materials, microelectronics and semiconductor materials, new optical materials, and optoelectronic materials in the near future. At present, China has entered the industrialization stage in the infrared window and wear-resistant coating, and has formed a high-quality technical group. Of course, compared with foreign countries, China started late and many technologies are still immature. 3.5 Enhancement Technology Nano-diamond is used as a filler for polymer materials, which can significantly increase its wear resistance and toughness. According to foreign reports, in the aircraft and shipbuilding industry, nano-diamond can be widely used in polyurethane rubber, nitrile rubber, polyisoprene rubber, styrene-butadiene rubber to make room temperature gaskets, low temperature gaskets and mechanical rubber parts. The wear resistance, tear strength and fatigue resistance of the workpiece can be comprehensively improved, and the friction coefficient can be reduced, so that the service life of the workpiece is increased by 1.5 to 3.0 times. China has also had research results in this aspect. The research of the Armored Force Engineering Research Institute shows that the nano-diamond is added into the binder to make a metal tonic, the tensile strength is increased by 72%, and the torsional strength is increased by 20%; The addition of nano-diamond to the rubber for tires can greatly increase the burst strength of the tire (from 53 MPa to 154 MPa). Since 1988, the Northwest Institute of Nuclear Technology has carried out research and development in this area. The results show that several common rubber materials with nano-diamonds have greatly improved the strength and wear resistance, and at the same time slowed down the aging phenomenon. occur. The composite plating layer such as stamping die and tool is made by using the plating solution containing nano diamond, which can greatly improve the hardness and wear resistance, thereby improving the service life of the tool. The domestic Huaqiao University, China University of Geosciences, the Academy of Armored Forces Engineering and the Beijing Institute of Mechanical and Electrical Engineering all carried out similar work and achieved good results. Nanodiamond ceramic materials can also be produced by explosive sintering.
4. Dispersion of nano-diamonds and its application in special functional coatings 4.1 Dispersion of nano-diamonds Although nano-diamonds have many of the above advantages and a wide range of applications, nano-particles have large specific surface area, high specific surface energy, and are thermodynamic. In an unstable state, agglomeration is apt to occur, thereby losing some of its good physical properties as nanoparticles. Although the nano-diamond has a fine grain size, the presence of hard agglomeration and soft agglomeration in the preparation and post-treatment makes the nano-diamond grain size coarser and the application is restricted. Therefore, it is necessary to study the dispersion of nanodiamond in the medium. There are single crystal diamond particles and agglomerates of diamond particles in the nano-diamond powder. The single crystal diamond particles are distributed between 1 and 60 nm. The agglomerates are large and small, small tens of nanometers, large hundreds of nanometers, and even There are also micron grades. Figure 2 is an electron micrograph of the surface-treated nanodiamond produced by Gansu Jinshi Nano Material Co., Ltd. It can be seen that the crystal shape of the nanoparticles is relatively regular and the particle size is relatively uniform, but only a small part of the nanodiamond particles are in a single crystal state. Most of the rest are in agglomerated state, and the size of some agglomerates has exceeded the range of nanoparticles. Nano-diamonds have excellent effects on ultra-precision polishing of hard disk heads, lubricant additives, and filling and reinforcement of plastics and rubber. However, even in these areas under development, the application promotion situation is still not satisfactory. An important reason is that the problems of dispersibility, stability, uniformity and compatibility of the nano-diamonds in these non-aqueous systems have not been obtained. Very well solved. Therefore, the realization of nano-diamond deagglomeration and stable dispersion has important practical significance for exerting its excellent performance and promoting its application in some technical fields. Through the structural characterization of nanodiamond black powder, it is known that their surface adsorbs various oxygen-containing polar groups such as hydroxyl group, carbonyl group, amine group, carboxyl group, ether group and ester group, which is caused by this layer of "coating". It is hydrophilic. For most polymers, they are exactly hydrophobic. In order to have good dispersibility and compatibility in the polymer, the black powder particles must be modified by external force (physical or chemical) to make the surface oleophilic and hydrophobic. In recent years, researchers at home and abroad have explored the dispersion of nanodiamonds in different media. Generally, the surface modification of the nanodiamond is carried out by a chemical-mechanical method, and the surface properties of the dispersion medium and the nanodiamond are adjusted by adding an inorganic electrolyte, a surfactant, etc., while the ultrasonic dispersion and the mechanical force of the ultrafine bead mill are added. By using a combination of surfactants, the surface potential of the particles and the hydrophilic layer are adjusted to increase the electrical barrier and steric hindrance of the particles. Chiganova heats the nanodiamonds with a saturated aqueous solution of AlCl3, and the secondary particle size of the nanodiamonds in the resulting suspension is in the range of a few hundred nanometers. Researchers at JSCDiamondCenter ultrasonically disperse nanodiamonds in aqueous solution, and the average particle size of the agglomerates in the resulting suspension is around 300 nm. The center also studied the dispersion of nano-diamonds in non-aqueous systems. The surface of nano-diamonds modified with polyisoprene was used to prepare a suspension that was stable for about 10 days. Chen Wanpeng, Tong Yi, et al. [The theoretical analysis of the causes of nanodiamond agglomeration, and the dispersion of nanodiamonds in aqueous and oily media, the particle size of the agglomerates reached 257.5nm and 44.9nm. Xu Xiangyang and Wang Baichun of the Changsha Research Institute of Mining and Metallurgy used a combination of anionic surfactants and nonionic surfactants to study the dispersion of nanodiamonds in aqueous media, and obtained the particle size of nanodiamond agglomerates. The average is below 100 nm, of which 25.7 nm particles account for 83.5% of the effect. Wen Chao of the Northwest Institute of Nuclear Technology studied the dispersion of nano-diamonds in aqueous media. Three special dispersants were prepared. Nano-diamonds were added to them, and then ionized water was injected. The fibers were dispersed for 30 minutes and allowed to stand for 60 days. There was no precipitation of nanodiamond particles in the suspension, and then the particle size was tested. The test equipment was a Malvern laser particle size analyzer. The nanodiamond agglomerate particle size can be dispersed to 10-20 nm and 100-200 nm in an aqueous medium by ultrasonic dispersion and a special dispersant. At present, the results of this research are only of research value because the efficiency of large-scale applications is too low. It can be seen from the above analysis that China's current de-agglomeration technology for nano-diamonds has not been completely solved, and many studies are still in the laboratory stage, and there are few real industrializations. If the problem of dispersion and storage stability of nano-diamonds in oily systems is solved, nano-_diamonds will have a very broad application prospect in the field of material reinforcement and special functional coatings.
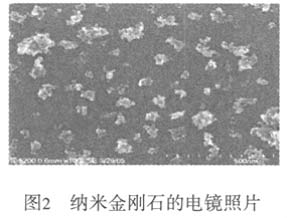
4.2 Application of nano-diamond in the field of special functional coatings and adhesives The sun's ultraviolet rays, acid rain, stones and bird droppings have a great erosion and damage to automotive paints. Due to the influence of these factors, automotive paints must have good protection properties, including: anti-corrosion, anti-stone, moisture, scratch, acid, chemical, solvent and so on. At room temperature, diamond is resistant to all acids, bases and solvents. Even at high temperatures, it resists all corrosion. Only strong oxidants can corrode diamond at high temperatures. Diamond also has the highest hardness, highest thermal conductivity and biodegradability. Therefore, nano-diamond can be widely used in automotive surface protective coatings, using the unique physical and chemical properties of diamond to improve the life of automotive paint. If the nanodiamond is used in the form of an additive or a mixed component, the appearance characteristics of the coating can be adjusted. Tests provided by a well-known foreign paint manufacturer show that the use of nano-diamonds not only increases the micro-hardness of the coating, but also makes the coating resistant to impact and scratches, and is more adhesive to the substrate than conventional coatings. Chemical resistance (especially solvent resistance), anti-friction, water resistance and thermal conductivity have been significantly improved. There are also reports in foreign countries that nano-diamond can be applied to the silicone coating of the fuselage, wing and hull surface of aircraft and ships, which can enhance the anti-corrosion, anti-freeze, temperature and aging resistance of the coating, and improve the elasticity and fracture. The strength and tear strength increase the service life of the surface coating by 1.5 to 2.0 times, and the cost is only increased by 1% to 2%. However, the application of nano-diamond in surface protective coatings has not been reported in China. Nanodiamond materials are also widely used in radar, infrared and visible light stealth. Foreign research in this area has been carried out for many years, and countries such as the United States have applied ultra-fine diamond as a absorbing material to stealth aircraft. Adhesive coating technology refers to the technology of adhesive coating on the surface of parts to achieve a special purpose. It is a development of bonding technology. Nanoparticles can effectively improve the performance of adhesives due to their excellent properties. Epoxy resin has higher adhesion and cohesion. Adding nano-diamond to polymer can improve its strength, wear resistance and heat aging resistance. When nano-diamond is added to the epoxy resin adhesive, the breaking strength is increased by 2.0 to 2.5 times. Diamond-containing nano-adhesives have excellent wear resistance and high bond strength. Table 2 shows the test results of the influence of nano-diamond particles on the wear resistance of the adhesive. The test results of the influence of nano-diamond on the tensile strength and tensile shear strength of the adhesive are shown in Table 3. Table 2 Effect of Nano-diamond Addition on Adhesiveness of Adhesives
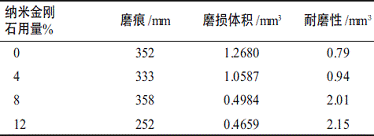
Table 3 Effect of nano diamond addition on the performance of adhesive
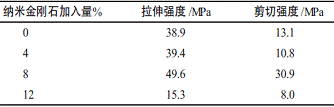
It can be seen from Table 3 that as the amount of nano-diamond added in the adhesive increases, the tensile strength of the adhesive increases. When the addition amount is 8%, the tensile strength is increased by 27.5% compared with the unadded, and the amount of addition continues. When the diameter is increased, the tensile strength decreases, and the addition of nano-diamond to the adhesive has little effect on the shear strength. Therefore, nanoparticles have broad application prospects in the field of surface coating and bonding technology. When nano-diamond is used in the field of special functional coatings and adhesives, it is not simply dispersed and added, and it needs to be surface treated to solve the disadvantages of difficulty in dispersion and poor stability after dispersion. There are two general surface treatment methods: one is to modify it with a surfactant, and such research is carried out in China, and most of them are applied to aqueous systems; the other method is surface coating of nanodiamonds. Cover modification, this method can solve the problem of dispersion of nano-diamond in oily system, but there are few reports in China. Bai Bo et al. obtained the PANI/nano-diamond composite microspheres by in-situ emulsion combined with nano-diamond and polyaniline (PANI). In the composite, the nano-diamond crystals were cubic and PANI was amorphous. The composite has a particle size of 10 to 30 nm, good dispersion performance, substantially spherical shape, specific surface area of ​​270 m 2 /g, and good thermal stability. The material has wide application value in the field of absorbing wave and electrostatic shielding.
5. Problems and Prospects of Nano-Diamond in the Application of Special Functional Coatings At present, nano-diamond technology is in a stage of rapid development, and its achievements have already shaken people. Because nano-diamond has peculiar physical-mechanical properties, it is a material with important theoretical research and application research value. People use the theory of physics, chemistry, materials, electronics and other cross-scientific studies to comprehensively study the properties of nano-diamonds, which will strongly promote the wider application of nano-diamonds in machinery, materials, electronics, energy and other fields. At present, the domestic nano-diamond production technology has approached or reached the international advanced level, but its application is still in the theoretical and laboratory stages. Only a few areas have completed the industrialization promotion work. Therefore, it is necessary to seriously study and implement how to Based on the existing research work, we will seize the opportunity to realize the industrialization of nano-diamonds and their applications in various related industries as soon as possible. In the process of industrialization of nanodiamonds, the following problems exist. (1). The current problem of dispersion and storage stability of nano-diamond powder still restricts its wide application in various fields. (2) At present, domestic nano-diamonds have certain research and application in lubrication, grinding, electroplating, CVD film, etc., but the research and application in material enhancement and coating performance improvement are slow, and there is a big gap with foreign countries. (3). Because nano-diamond is more expensive, its application in general civil coating products will be limited, but in the field of protective special and military coatings, the performance of coatings is more important. The cost of coatings is not the primary. Position, therefore, we should vigorously strengthen the research and development and application of nano-diamond in the field of protective special coatings and military coatings. (4). From the experience of foreign use, nano-diamond has been widely used in radar, infrared and visible light stealth and achieved ideal results, and China's research in this area has not been reported.
Other Belts
Rubber Belt,Belt Conveyor,Conveyor Roller
Perforated Metal Sheet,Belt Co., Ltd. , http://www.nslinkfence.com