Importance of safety and protection in welding production
Welding production inevitably produces soot and toxic gases. If it is not collected and disposed of, it will cause pollution damage to the working space, directly threatening the safety and health of the employees, and will also aggravate the negative impact of the atmospheric environment. The harmful substances generated in the welding production are composed of fine-grained dust bodies mixed in various gases, 90% of which are from the welding materials used, and a small amount is generated from the welding base material. A gaseous substance that may contain nitrogen oxides, carbon monoxide, ozone or formaldehyde, combined with fine particle oxidizing substances that may contain iron oxide, magnesium oxide, manganese oxide, chromium oxide, cadmium oxide or aluminum oxide, is highly susceptible to floating and diffusion, and belongs to the human body. Inhalables (mostly <PM2.5) will deposit in the lungs and are irreversible. These harmful smoke and dust substances cause human discomfort and health disorders, and can cause serious poisoning or even death, such as chronic manganese poisoning and electric welders' silicosis. Hexavalent chromium compounds, nickel oxide, cadmium oxide, cerium oxide, cobalt oxide, etc. are all carcinogenic, and the accumulation of a certain concentration of Al dust can cause burning or explosion accidents. It can be seen that the collection and treatment of welding fume is crucial for people-oriented, energy-saving and income-increasing, environmental improvement and safe production.
Main products and core technologies
With nearly 100 years of history, the American Donaldson Group is committed to the development and development of leading filtration technologies and products. It has unique patented technology products and many successful application cases in machining ventilation, dust removal and flue gas treatment, especially for traditional manuals. There are practical solutions and treatments for welding and automatic welding, such as welding, brazing, pressure welding and soot collection and processing of robotic welding processes in the ever-changing development. The advanced nature of Donaldson's ventilation and dust removal technology products is mainly reflected in the patented filter material with higher dust collection efficiency, the scientifically designed airflow uniform dust collector body and the mature process layout and consideration.
First, the choice of Ultra-WebFR filter: For the treatment of welding fumes, the Ultra-WebFR flame retardant filter material developed by Donaldson became the core of Donaldson's high-efficiency and low-resistance dust collector, as shown in Figure 1. The filter material of the filter element is coated with a special nanometer-diameter special microfiber on a selected conventional filter material to form a filter material having a very small pore diameter and an extremely high opening ratio on the surface. It can effectively block most sub-micron particle dust, and can provide relatively high filtration efficiency. For 0.2~0.5mm soot particles, the dust collection efficiency can reach 99.999%, and improve the backflushing function, so that the dust collector can maintain one. Longer run at lower differential pressures.
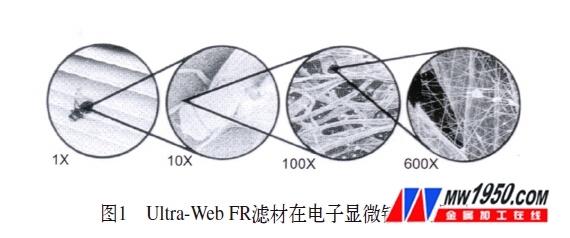
Secondly, Donaldson attaches great importance to the research and development of new products and new technologies, and invests considerable funds in this work. The purpose is to continuously meet the increasing demand for ventilation dust collection and environmental protection industry development, and to lead the international advanced industry position. In line with the welding process, the form of the dust collector is also timely and innovative, providing users with a more cost-effective product, while making the use more convenient, and the discharge standard is more practical. For example, the Donaldson Torit brand DFO type dust collector, which is marketable in the domestic and international markets, is the result of uninterrupted innovation and improvement, and has been well received by customers. This modular dust collector adopts Donaldson's unique patented sinking structure. Its working principle: the negative pressure air flow generated by the dust-containing airflow through the fan enters the dust chamber through the pipeline, and the soot particles separated by the filter cartridge are blocked by the filter element. On the surface of the filter material, the purified air enters the clean room and is emptied. When the blocked dust is continuously deposited on the surface of the filter element, the pressure difference inside and outside the filter element is also continuously increased. When the pressure difference reaches a preset value, the solenoid valve for controlling the compressed air is opened, and the compressed air flows back through the pipe. The cleaning system is instantaneously sprayed onto the inner surface of the filter element, so that the dust particles deposited on the outer surface of the filter element are separated from the filter element by the high-pressure airflow and dropped into the dust collecting barrel, and the surface of the filter element is cleanly regenerated.
Tests have shown that the Downflo ® Oval type dust collector (see Figure 2) is more evenly distributed than the Downflo ® II type. The Downflo ® Oval type can handle larger air volumes and run more smoothly than the same filter element. Extended service life.
With the rapid development and advancement of the welding and cutting industry, Donaldson has developed the PowerCore series of products, including TG-type dust collectors, which have been widely used in welding, plasma cutting and laser cutting, highlighting compact size, small footprint, and operation and maintenance. Simple and efficient dust collection (see Figure 3). This TG type dust collector adopts the principle of submerged filtration, and adopts Donaldson's patented Ultra-WebFR flame-retardant filter material, and the filtration efficiency reaches Merv13 grade. The dust collector integrates the spark thrower, fan/motor and nozzle, and is also more convenient for transportation, installation and maintenance.

Production practice shows that to ensure the successful operation of the welding fume control system, it is more important that the design of the entire dedusting system and the matching of the matching settings are correct and the layout is reasonable. This requires suppliers not only to provide the required dust collector body, but also to have rich field experience, mature application skills and product integration information, from suction hood, pipe network layout, dust collector body, to fan power / pressure calculation, etc. Design selection is based on solid standards or guidelines. Taking the dust occurrence point as the main target of the treatment, the vacuuming method can be divided into a top suction type, a side suction type, a blow suction combined type, and a mobile type. The characteristics of the welding process, actual site conditions, space constraints and governance standards and requirements are the main factors in the development of the plan, must be carefully considered, and use the available products and technologies. The main application examples of the product are shown in Figures 4-8.
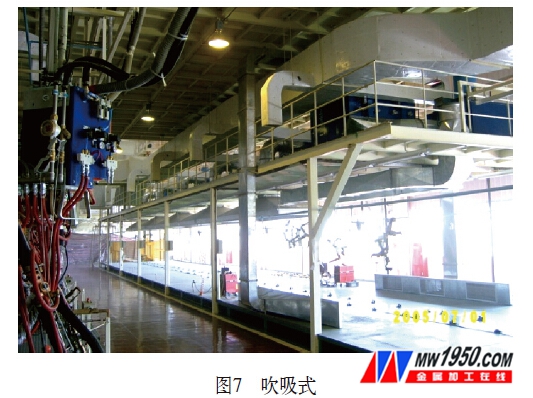
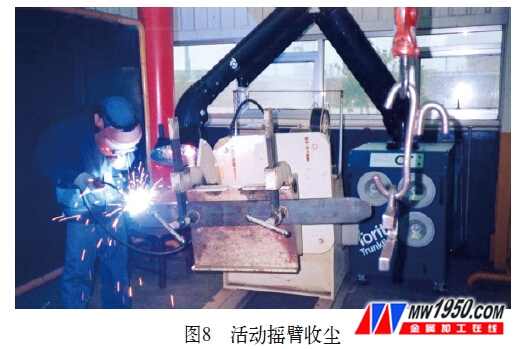
In order to meet the collection of welding fumes, it should be considered to consider the use of flame-retardant filter materials, the installation of spark throwers in the pipeline system; the collection of explosive dust should increase the venting device in the system, necessary fire-fighting facilities; When generating static electricity, it is also necessary to consider the use of static elimination filter material. The body of the dust collector is grounded according to the standard requirements. Only on-site factors are considered in place, such as the effects of welding heat diffusion, ambient airflow field on the ventilation and dust removal system, and the correct dust collector and surrounding accessory products are selected, and the welding fumes can be controlled to achieve the preset effect. Manufacturers who rely on the welding process can seize the provider that meets the equipment improvement, recognize the crisis and take correct and effective measures to build up the next level.
More exciting content Welcome to Metalworking Online》》》Essen Special Report

The 19th Beijing Essen Welding & Cutting Fair
Sofa
sofa table,sofa set,sofas on sale, sofa chair,Living Room Furniture
The sofa table application place is Office Building, Livingroom,Other, and Material use Fabric and metal, Design Style is Modern
Place of Origin: Guangdong, China
Usage:Livingroom Furniture
Specific Use:Living Room Sofa
General Use:Home Furniture
Regional Style:European style
sofa table, sofa set, sofas on sale, sofa chair, Living Room Furniture
Duraplex Limited , https://www.fsduraplex.com